Concrete Resurfacing – Repair of Concrete Floor or Pavement Surfaces
Concrete resurfacing is a method of rehabilitation of tone or damaged concrete floor or pavement surfaces to make it available for use without the reconstruction of the whole structure.
Before undergoing any kind of method as a part of resurfacing of concrete, it is necessary to conduct an evaluation of the existing surface. This evaluation is to find whether the existing layer satisfies certain design considerations.

Requirements of an Existing Concrete Pavement Surface
As mentioned above, there are certain considerations which have utmost importance before undergoing resurfacing. They are:
1. In order to carry out the needed service, the existing layer must have adequate thickness.
2. The concrete surface might have longitudinal as well as transverse joints. These joints must be able to transfer to load smoothly to the underlying layer (Soil). This load transfer must be done without affecting the smoothness of the surface (Once the resurfacing is carried out).
The penetration of fine solids or moisture has to be restricted by the joints or cracks present through the resurfaced layer or through the underlying pavement and the resurfacing.
3. In order to face severe exposure conditions, adequate cover has to be provided for the reinforcement. The reinforcement must possess a size and spacing in order to make the crack present to be tight.
4. The maximum size of aggregates used in the service is based on the thickness of resurfaced layer and the steel spacing.
5. Good and Durable aggregates have to be employed. In areas where there are chances of freezing and thawing problems, it is recommended to have air entrainment. The use of salts in order to de-ice can also be employed.
6. The material used for the construction of shoulders must be either concrete or other stabilized materials, in order to avoid chances of infiltration of shoulder materials in between the underlying pavement and the resurfacing layer.
Evaluation of the Existing Concrete Floor or Pavements for Resurfacing
As mentioned before, the condition of existing pavement must be evaluated before carrying out the resurfacing procedures.
The three basic elements of the evaluation of the existing pavements are the:
- Evaluation of the functional condition or the Serviceability Condition
- Evaluation of the distress through surveys
- Evaluation through Structural Testing
The three of the mentioned criteria are not mutually exclusive to each other. They can either occur individually in an existing pavement or in a combination. This different condition of occurrence influences the decision behind the resurfacing.
The major factor behind the selection of best overlay option is by understanding the true condition of the existing pavement or surface. The true evaluation must give a picture on how it will behave when a new overlay is laid over the existing one. This condition is based on structural evaluation rather than functional evaluation.
Major points behind the evaluation of the existing pavements are explained below:
Functional Adequacy of the Old Surface
Serviceability condition is mainly related to the surface of concrete subjected to traffic. This is the condition of the pavement based on the ride quality. Evaluation method makes use of panel ratings. Some of the agencies evaluate based on the ride quality. One such example is the response type ride quality measurements.
An overlay surface may be provided due to the functional inadequacy of the old surface. This surface can be provided to improve the skid resistance of the surface. When the pavement surface does not follow one or more levels of service, then a functional overlay can be provided.
For functional overlay, the minimum thickness of the overlay surface will be that needed to have construction convenience or to bring the surface to an acceptable level of service.
Distress Surveys
The nature and the extent of damage to the existing layer can be determined through the distress surveys. This data provides us an idea on the performance of the resurfacing layer. Different methods are employed as a part of the survey. But a standard method has not been put forward yet.
The most popular method employed are the Pavement Condition Index (PCI) and Concrete Pavement Evaluation System (COPES). The PCI method is employed for flexible pavement. The COPES is used for concrete pavements.
A manual named Highway Pavement Distress Identification Manual was used and followed in the past.
Structural Adequacy
The famous Non-destructive testing is employed to understand the structural adequacy of the existing surface layer. This is through the evaluation response from the pavement to the applied loads. There is a relation between the nature of the response and the structural adequacy of the pavement.
AASHTO have developed another approach which is named as “remaining life”. This as the name tells, will evaluate the life that is consumed from the pavement. The measure of consumption can be either based on time or based on the number of loadings. This method gains limitations of error in the measurement of remaining life. It can show a higher or a lower value without any kind of reason.
Another approach was again put forward by AASHTO (Third Approach). This will make use of the distress surveys and the material properties of the existing pavement to determine the structural capacity of the layer.
The Structural Design of the Pavement or Floors for Resurfacing
When comparing the structural deficiency and the functional deficiency, the former will override the latter. This is because the thickness that is demanded by the structural deficiency to be solved will be anyway greater than the thickness that is demanded by the functional deficiency.
The resurfacing thickness design involves many approaches. But it involves the determination of the following requirements:
- Structural Capacity: Determination of the capacity that will account the prevailing and the estimated future traffic for the design life planned for the resurfacing layer.
- Effective structural capacity or the In-situ structural capacity
- Difference between the structural capacity and the effective structural capacity
Other Requirements in Concrete Resurfacing
Some of the other factors that will be a concern during the resurfacing are mentioned below:
Interface Between Concrete Layers
These forms the area between the underlying layer and the overlay surface. This a very important concern in the design consideration. The nature of bond is judged by the interface. This bonding will affect the performance of the whole resurfacing layer.
When talking about interface materials, they serve mainly two purposes. The interface material either will improve the bond between the underlying layer and the resurfacing layer. Or they can be used to separate the underlying layer and the resurfacing layer.
The first purpose will make the two layers to behave monolithically under load action and transfer. The second purpose will make the individual elements to act as separate elements. The second purpose means there is a little or no kind of connection between the two layers.
Based on this we have bonded resurfacing and Unbonded resurfacing.
Bonded Resurfacing
The bonded resurfacing mainly makes use of plain cement concrete slurry or grout to serve the purpose of the bond between the old and the new layer. The preparation of the grout is carried out in a mobile mixer.
The materials used are Portland cement and water. Mainly the water cement ratio used is not greater than 0.62. In certain areas, these are not used. But instead of grout, the resurfacing material is itself used as bonding interface material. They are applied on a clean surface. The method proved to be efficient in increasing the bond and durability in its performance.
Unbonded Resurfacing
Unbonded resurfacing is mainly used in conditions where the underlying layer is very weak and have high distress. In such a condition, if a bond is made between the new overlay and the old a problem of reflective cracking is said to occur.
This is because the stress in the weak bottom layer gets transferred to the new top layer. Hence under such situations, an unbonded interface material is used. This will hence make the two layers to act and perform individually.
To have such a positive layer, numerous materials are available. Some of them are asphalt-aggregate mixtures of various type and the polyethylene, Other materials are wax based curing compounds and liquid asphalts. Initially, a liquid asphalt layer that is covered with a polyethylene sheet was preferred.
It is also specified to use thick layers of surfacing than thin layers. Thin layers can also create chances of reflective cracking in the overlay. The below shows the recommendations for asphalt unbonded surface layer provision in different conditions:
- In the case of the underlying pavement have joint or crack that is greater than 6mm, and also deterioration of slabs and spalling is highly evident; an asphalt layer of a thickness not less than 25mm have to be provided.
- In case the faulting and slab deterioration is not evident highly, a thin layer of asphalt is provided of a thickness not greater than 13mm. A slurry seal material can also be employed that have a nominal thickness of 3mm. This thin layer must be able to cover all the defects that are reflected on the surface of the existing (damaged) pavement.
- In the case where the fault and cracks are not evident, a slurry seal of a minimum thickness of 3mm is provided. Or an asphalt layer that is followed by a sand cover can also be recommended.
The figure below shows that the inadequate thickness of the layer will not prevent keying of the overlay.
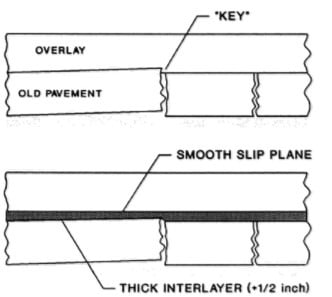
Fig.1: Before and after providing interface material between the damaged and the new layer
Drainage for Concrete Surface
It is a need for the provision of cross slopes in the pavements to facilitate proper water drainage. But now it has been necessary to bring texture to the pavement surface to gain proper and efficient skid resistance also. It is also recommended to provide a subsurface drainage facility when a resurfacing is carried out.
During the evaluation of the pavement, the designer is asked to evaluate the existence of joint faults, pumping, corner breaks or any other kind of distress in the pavement. This is usually reflected in the PCC pavement.
In the case of AC pavements, distress is like fatigue cracking and potholing. Any symbol of moisture affected distress implies that the drainage system is inadequate. So, before the overlay construction, proper drainage must be maintained.
In the case of an interface layer that is not bonded, open-graded drainage layers will behave well as the interface material.
Reinforcement for Concrete Resurfacing
Certain pavements will make use of reinforcement as distributed deformed steel. This will ensure the control of the various type of cracking. The cracking thus observe is a result of joint spacing.
This is mainly due to the shrinkage that is related to the hydration reaction of the Portland cement (drying shrinkage). This varies with the temperature and the slab’s moisture content.
The reinforcement that is provided to the resurfacing is very much similar to that employed in the installation of a new pavement. The AASHTO 1993 provides the whole details on the same.
For overlays that are joined through joints, the slab length is the factor that will govern the reinforcement design. When the slab has a length lesser than 4.6m, reinforcement is not recommended. But in the case of slabs with long length, the reinforcement is provided with the cross-sectional area varying from 0.05 to 0.20 % of the slab cross section.
In the case of overlays that are concrete reinforced, longitudinal reinforcement must be provided to keep transverse cracks that are formed tightly closer. This will avoid the penetration of undesirable chemicals and carry out good load transfer. Here, the percentage of steel used is greater than that used for jointed overlays.
A minimum of 0.6% of a cross section of the slab will be required. Recent practice makes use of 0.9% of the cross-sectional area of the slab.
Joints in Concrete Floors and Pavements
The movements that are created in the pavements due to the variation in temperature and the change in concrete volume must be facilitated by providing adequate joints at desirable locations.
In the case of a plain cement concrete resurfacing, the joint location and provision are related to the type of interface that is used. When a bonded resurfacing is employed, it must match with the joints that are used in the underlying pavement layer. Any failure in this will cause reflective cracking on the new layer.
Hence, the performance of the pavement is reduced. But when the unbonded interface is used, an entirely different behavior is shown.
It is recommended that the transverse joints in the surface should have a mismatch if any by an amount of 0.6 to 0.9m (when compared with the original pavement). The joint has to match with the one in the underlying pavement. This consideration will help in the reduction of stress concentration and their related distresses.
Advantages of Concrete Resurfacing
- The concrete resurfacing act as a part of maintenance and longevity for the surface. This helps in prevention of cracks for a longer period and make the formation of potholes (In the case of driveways) loose its existence.
- The concrete possesses a light color which tend to control the temperature maintaining a comfortable cooling effect during summer seasons.
- Concrete resurfacing is now provided by staining with variety of color which adds aesthetic beauty to the surface.
- Variety of color options are available in the concrete resurfacing option. This can give a great look for the home exterior.
- The removal of snow from the concrete surface is found easier when compared with any other surface.
Disadvantages of Concrete Resurfacing
- Improper overlay and evaluation of the existing condition will bring the decision of concrete resurfacing to fail. This may lead to show the cracks on the surface. The only remedy for this is the complete removal of the pavement and construct a new surface.
- The choice is not found economical for larger areas.
Comments