Masonry Reinforcement and Accessory Metals for Masonry Wall Construction
Specifications for reinforcement and accessory metals used in the construction of masonry walls is provided by International Building Code (IBC 2009) and Building Requirements and Specification for Masonry Structures (ACI 530.1-11).
Various types of reinforcement and metal accessories is discussed in the following sections.

Fig.1: Reinforcement Placement in Masonry Wall

Fig.2: Reinforcement and Accessory Metals Employed in Masonry Wall
Masonry Reinforcement, its Types and Accessory Metals for Masonry Structure
Masonry reinforcement and accessories includes:
- Steel reinforcement
- Connectors
- Sealants
- Flashings
- Coatings
- Vapor and moisture barriers
Steel Reinforcement for Masonry Structure
Steel reinforcement used in masonry structure involves reinforcement bars, joint reinforcement, and deformed reinforcing wire.
Steel bars are utilized to improve both tension and compression strength of masonry structure.
Masonry bond beams, lintels, and walls are examples in which steel reinforcement are applied to improve tensile strength of the member whereas reinforcement bars are used in masonry column to increase its compression strength. Hot rolled deformed bars, which possess ribs on its surface to enhance bond strength, are employed in masonry structure.
As per ACI 530.1-11, the maximum reinforcement steel bar size is No.11. The restriction on the size of reinforcing bars depends on the accepted construction practice and performance of the masonry structure.
It is claimed that, using and distributing small size steel bars in masonry provides better performance compared with small number of large size reinforcement placed in the masonry structure. Figure-3 demonstrates installed deformed steel reinforcement bars in the masonry wall.

Fig.3: Utilization of Deformed Steel Bars in Masonry Wall
The steel reinforcement bars are usually categorized based on minimum yield stress of the steel which employed to manufacture the steel bars. Both epoxy coated and zinc coated steel bars are permitted to use in masonry structures and they may be utilized when corrosion protected reinforcement are specified as per the design.
Both epoxy and zinc coat protect steel bars in severe condition and consequently increase the life span of the structure.
If steel bars are covered with epoxy coat, then it is required to increase its development length and it should be 1.5 times the development length of uncovered bars. In contrary, bars covered with zinc coat do not need to increase the development length because zinc provides the same property as uncoated bars.
It should be said that, delivering and installation of coated bars need considerable attention to avoid coating damages otherwise the purpose of steel coating will not be achieved. So, any damages experienced by steel coating need repair prior to installation.
Figure-4 and Figure-5 show epoxy coated and zinc coated steel bars respectively.

Fig.4: Epoxy Coated Steel Bars for Masonry Structures

Fig.5: Zinc Coated Steel Bars for Masonry Structures
The fiber reinforced polymer bars can be employed in masonry structures as a replacement of both zinc and epoxy coated bars in aggressive environments.
Figure-6 provides different types of fiber reinforced polymer bar. The FRP bar are available in different sized and they are considerably light which is advantageous because it substantially decreases the cost of delivering, handling, and installation.

Fig.6: Various Types of FRP Bars for Masonry Structures
Regarding joint reinforcement, there are three types of joint reinforcement involves welded wire fabric, deformed reinforcing wire, and ladder or truss type joint reinforcement.
Joint reinforcement is provided for different reason for example increase the size of a panel, increase the spacing between movement joints, and control differential movements. Added to that, it improved horizontal bending and restricts cracks in masonry structure. Joint reinforcement applications are shown in Figure 7 and Figure 8.
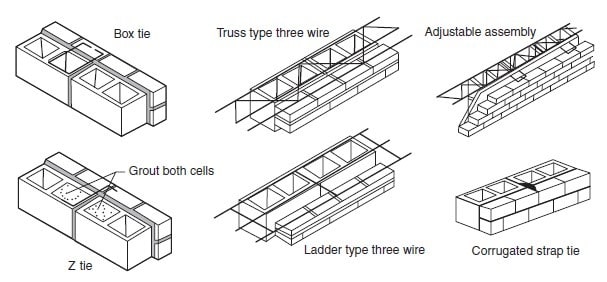
Fig.7: Joint Reinforcement Applications in Masonry Structure Construction

Fig.8: Installation of Joint Reinforcement in Masonry Walls
Connectors for Construction of Masonry Structures
There are various types of connectors which are used to connect or secure two members or parts together. For instance, ties can joint two Wythe’s of masonry wall together and adjustable ties may be employed to make rooms for differential elevation in masonry bed joints.

Fig.9: Types of Adjustable Pintle Tie Used in Masonry Structure

Fig.10: Types of Veneer Tie Employed in Masonry Structure

Fig.11: Types of Connectors Used in Masonry Structure
Sealants in Masonry Walls
Sealants are employed to fill and seal the spaces or joints which are created deliberately in masonry walls for specific purposes. There are three major joints in masonry structures includes construction joints, expansion joints, and control joints.
Sealants are usually produced from manmade polymers such as latex, silicone, neoprene, and butyl rubber. The elastic property of sealant including compressibility is equal to ratio of minimum thickness to original thickness.
Based on the anticipated service life of sealants, deteriorated sealants need to be replaced by new ones. It is claimed that, ordinary life span of majority of sealants, which are placed at exterior face or walls are around seven year.
The main factor behind sealant deterioration is due to sealant exposure to ozone and ultraviolet light. This is because polymers which are utilized to manufacture sealants are damaged under such conditions.
Figure-12 illustrates the application of sealants in the masonry wall joint, and Figure-13 shows sealant before and after the masonry wall expansion.

Fig.12: Use of Sealant in Masonry Wall Joints
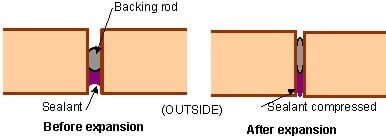
Fig.13: Employing Sealant in Expansion Joints of Masonry Wall
Flashings for Construction of Masonry Walls
Flashing is changeable and adaptive watertight material that may be manufactured from copper, stainless steel, plastic, plastic coated aluminum, and rubberized asphalt.
The life service of metallic flashing is considerably longer than plastic flashing that is prone to tearing. Rubberized asphalt flashing, which adhere itself to the masonry, can be installed easily and demonstrate reasonable durability.
Flashings are installed at different location of masonry walls, for example, all interrupted drainage cavity, bottom of each story level, under the sills of windows and doors, and over lintels of windows and doors.
It is applied to drain water that penetrate external Wythe of masonry wall. Weep holes at spacing of around 61cm above the level of flashing.
Figure-14 shows the installation of flashing and weep hole exactly above it in masonry wall.

Fig.14: Installation of Flashing in Masonry Wall
Coatings for Masonry Structures
Masonry structure Coating involves application of paints and water repellent coatings. Comparatively, the effect of water repellent admixture is better than that of water repellent coatings.
The latter cannot bridge considerably wide cracks but rather it traps water behind them and consequently damages behind coating will occur due to freezing and thawing affect.
Vapor and moisture barriers for Masonry Structures
Vapor barrier is a watertight membrane applied to prevent the vapor or water penetration into masonry walls and consequently avoid interstitial condensation inside the air space of drainage wall.
The vapor membrane is used for exterior face of inner Wythe wall in warm conditions whereas it is applied for the interior surface of outer Wythe in cold condition. This is because warm air around the structure can go though outer Wythe and condense within the inner Wythe while in cold condition warm air inside the building will pass through inner Wythe and condense in the cavity.
Vapor barrier are practically applied for outer face of inner Wythe.
Moisture barrier impedes water penetration into the masonry wall whereas it does not prevent vapor penetration and hence it allows condensation in air space of drainage wall.
Comments