How to test Hardened Concrete for Quality of Construction
Hardened concrete gains strength with time and testing these hardened concrete for quality check is important for structures. Different types of tests are available to check different properties of hardened concrete which are discussed.
Properties of Hardened Concrete
- Early volume change
- Creep Properties
- Permeability
- Stress-Strain Relation
Early Volume Change (Shrinkage) may result in cracking. Plastic Shrinkage occurs due to water loss from fresh paste by evaporation or from suction by dry surface. Volume decreases up to 1% when the paste is still plastic. Controlling water loss may help to prevent plastic shrinkage of concrete.
Drying Shrinkage occurs due to loss of water and/or cooling. 15-30% of dry shrinkage occurs in the first 2 weeks, 65-85% in first year. Drying shrinkage can be induced by lack of curing, high water-cement ratio, high cement content, low coarse aggregate content and existence of steel reinforcement. It depends on size and shape of concrete structure and may be non-uniform due to non-uniform loss of water.
Swelling may occur if concrete is cured continuously in water after settling. Its effects are relatively small and does not cause significant problems.
Stress-Strain Relation of hardened concrete is shown in figure below:
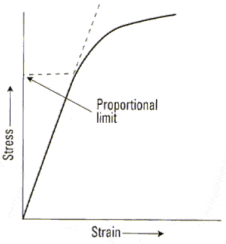
Aggregate and cement paste individually show a linear stress-strain, due to micro-cracking between the aggregate and cement paste interface, but concrete is nonlinear. For structural design, we need compressive strength (fc) and modulus of elasticity (E).
Tests on Hardened Concrete
Tests performed on hardened concrete are:
- Compressive strength test (most common) – DT
- Modulus of Elasticity – NDT
- Split-tension test – DT
- Flexural strength test – DT
- Rebound hammer test – NDT
- Penetration resistance test – NDT
- Ultrasonic pulse velocity test – NDT
- Maturity test – NDT
Compressive Strength Test (fc’)

ASTM C39: Cylindrical specimen (6 in. by 12 in.) is used for this test. For normal-weight concrete: fc’ range is 21 MPa to 34 MPa (3000 psi to 5000 psi). Compressive strength depends on specimen size, larger specimens has greater probability for weaker elements, reducing strength and have less variability and better representation of actual concrete.
How does failure occur?
Weakest location of hardened concrete is the interface between cement paste and aggregate
Modulus of Elasticity – Ec Test on Hardened Concrete
ASTM C469 is used to determine the chord modulus. 3-4 loading steps are needed in this method. Same sample is used. This method provides a useful relationship with strength. The range of test result is 14 GPa – 41 GPa (2000 ksi to 6000 ksi).
Poisson’s Ratio is determined using ASTM C469. Range is between 0.11 to 0.21, depending on aggregate, moisture, age, and compressive strength.
Split Tension Test on Hardened Concrete

Split tension is computed by T = 2p/BLD
where:
T = tensile strength, MPa (psi)
p= load at failure, N (psi)
L = length of specimen, mm (in.)
D = diameter of specimen, mm (in.)
Tensile strength varies from 2.5 MPa to 31 MPa (360 psi to 450 psi), about 10% of compressive strength
Flexure Strength Test (ASTM C78) on Hardened Concrete

Calculation of Modulus of Rupture
If the fracture occurs in the middle 1/3 of the span
R = PL/(bd^2)
Where:
R = flexure strength, MPa (psi)
P = maximum load applied, N (lb)
L = span length, mm (in.)
b = average width of specimen, mm (in.)
a = average depth of specimen, mm (in.)
If fracture occurs further outside the middle third, the results must be thrown out
Useful relationships:
- R = (0.62 to 0.83)fc’^0.5 (S.I. units)
- R = (7.5 to 10)fc’^0.5 (English units)
Rebound Hammer Test (Schmidt Hammer Test) on Hardened Concrete

Use a calibration chart graphs supplied to related the rebound to strength. 10 to 12 reading are performed per specimen. The test is used to test the uniformity of the concrete.
Penetration Resistance Test (Windsor Probe Test)
It is a non-destructive test. Gun-like device shoots probes into the concrete’s structure. It is performed on each of three holes in a special template. An average depth is then found. Depth is inversely related to the strength. It gives a better estimate than the rebound hammer.
Rebound hammer tests only the surface while penetration resistance test make measurements into the depth of the sample
Ultrasonic Pulse Velocity Test (ASTM C597)
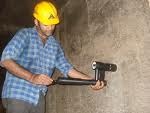
Maturity Test (ASTM C1074)
Maturity is the degree of cement hydration which varies with time and temperature. It is assumed that the strength is a function of maturity for a particular concrete mixture. Devices are used to measure the temperature of concrete with time.
Permeability Test on Hardened Concrete
This test affects the durability of hardened concrete and allows water and chemicals to penetrate its surface. It causes reduced resistance to frost, alkali-aggregate reactivity and other chemicals, corrosion of steel rebars.
Air voids that affect permeability are obtained from incomplete consolidation of fresh concrete, evaporation of mixing water that is not used for hydration of cement. Increasing the water/cement ratio has strong effects on permeability. Other factors affecting permeability are age of concrete, fineness of cement particles, air entraining agents.
Creep Properties of Hardened Concrete
Creep is the gradual increase in strain, with time, under sustained load. It is a long term process (several years) and vary with type of structure. It causes increased deflection and increased stress in steel, gradual transfer of load from concrete to steel and losing some of the prestress force in prestressed concrete.
Comments
Elcometer
What Is Plain Cement Concrete (PCC)